
Medford, OR is the home of Harry and David, a mail order company that specializes in pears, apples, chocolates and a popcorn and nut mix called Moose Munch®. This is their outlet store.

We boarded a small bus to go on a tour of their production facility.

Pears are the mainstay of their company so pear logos are everywhere. This is the lobby floor of their packing warehouse.

The warehouse is mainly one large room. This is half of it.

July through December is the high season for them so there wasn't much going on when we went through. Here baskets are packed with cookies, Moose Munch® and cake.

The quality control gal (in blue vest) is redoing baskets that don't meet the requirements.

In between buildings was the forklift highway. This end led to the freezers.

This end led toward the supplies area.

We went through the bow tying area where they hand-tie all the bows.

Here they are packing boxes with treats for Mother's Day shipments.

At the end of the line, the boxes were ran through the tape machine.

Here cookies are being packed into baskets then an air bladder was placed between the handle and the cookies to protect them from damage during shipment. Harry and David tried

hard to be a green company. The air bladders are made of a type of plastic that degrades in a couple years. The lights over the walkway were motion activated.

Looks like Moose Munch, Bing cherries and truffles are being packaged up on this line.

The boxes are stacked into towers.


Here is where the pears come into the facility and are sorted. Only the most perfect, damage-free pears are sold as their Royal Riviera® pears. One with damage are sold as comice at their store or sold to other places.

People that have been there long-term get their own numbered parking spot.

The bus went past their nearest orchards.

Oh yes, the place to be... the candy factory.

Once again the floor had a pear motif.

Ok this is the start of the Moose Munch®... popcorn. On the far right popcorn is loaded into a hopper. The white hose sucks it into the popper (large steel box in center left).

It is rolled through the sieve as it comes out of the popper. This gets rid of unpopped kernals and those too small for the mix.

The white scoops carry the popcorn along a conveyor.

Where it is dropped into a hopper.

It gathers into the hopper while below salt, sugar and butter are cooled into a syrup. Once the syrup is ready, the hopper dumps in the popcorn.

The popcorn is mixed in.
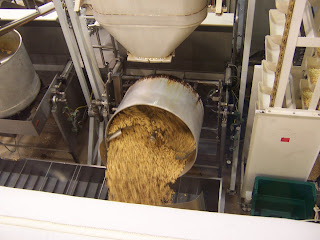
Once it is well mixed, the pot is dumped onto another conveyor belt where it is carried off to be packaged or processed further.

Then we walked into another area where pies are being made. The pans are two pieces. The bottom crust is pre-cooked to prevent it from getting soggy.

Fruit filling is dumped into this funnel where it is measured into the crusts.

This is where the pies actually start. Dough is ran through a machine to flatten it.

The gal takes it off to the side where she trims the sides. Then she rolled the cutter over it to make it into the side pieces for the pies.

Then we headed off the the enrobing room. We watched these pretzel chunks come down the conveyor.

Then they were enrobed in chocolate. I just stood here and drooled. Not that I like pretzels so much but... that chocolate!

Right after they were covered in chocolate, they ran under a "stringer" where white chocolate was striped across them.

In another room real pretzels were layed out be be enrobed.

At the end of the tour, the guide stepped up to a large tower and opened it to reveal a refrigerator.

We each got a box with two cream cookes and a mini mint truffle. Yuppie!